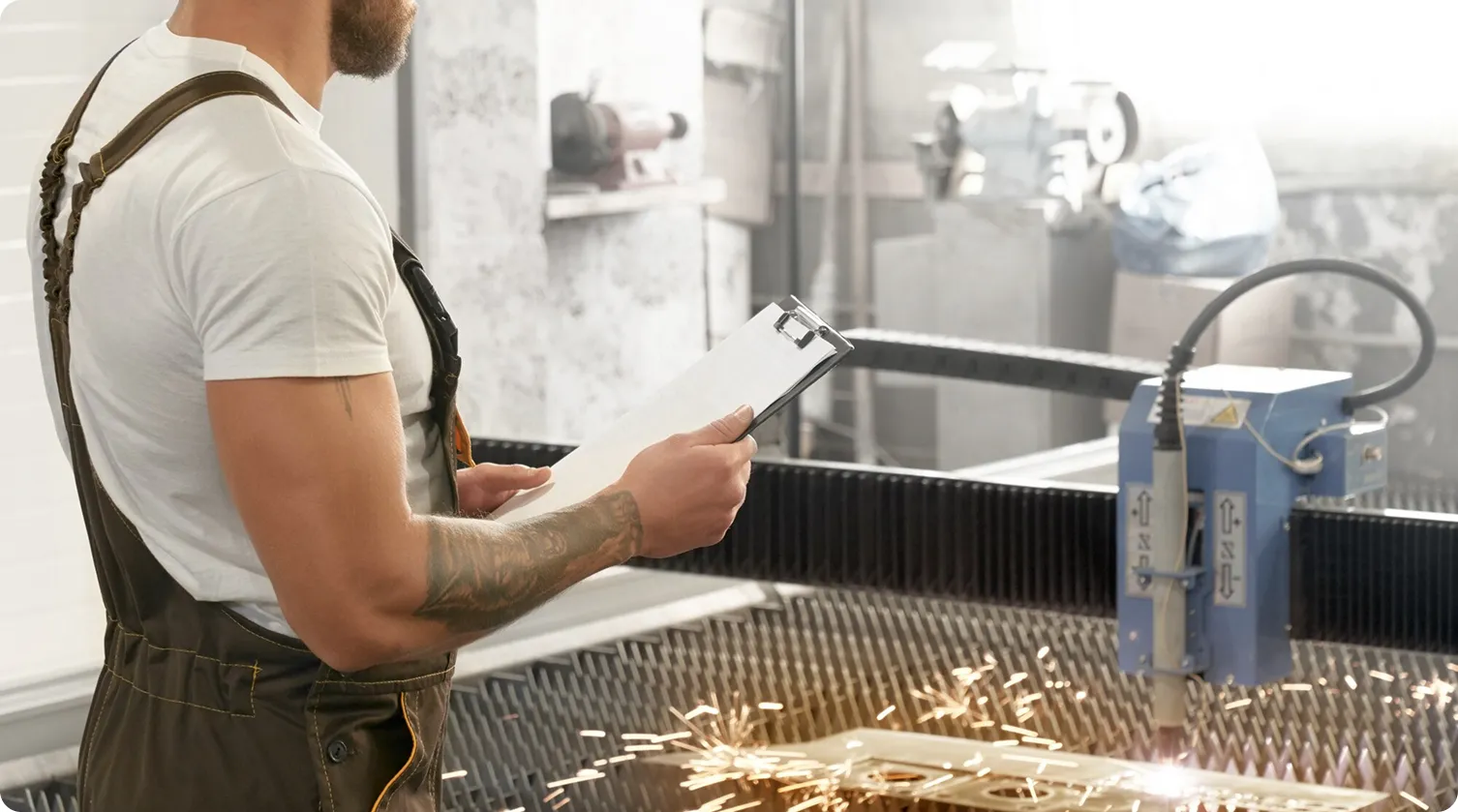
Welding Inspection Processes
Welding inspection at all stages ensures strong, safe joints by catching issues early and verifying final quality.
Introduction
Welding inspection is not a one-time task, but a continuous qualityassurance process that spans the entire welding workflow. At Insperia Solvex,we divide welding inspection into three key stages—before, during,and after welding—to ensure full compliance with engineering standards,structural requirements, and industry codes.
Each phase plays a distinct role in identifying and preventing defects,controlling variables, and ensuring that welded joints meet the design intentand safety expectations.
1. Pre-Welding Inspection
Before any welding operation begins, a detailed pre-weld inspection ensuresall preparations are complete and conditions are suitable for high-qualityresults.
Key Steps in Pre-WeldingInspection
- Review of client specifications, structural sensitivity, and required quality level
- Analysis of engineering drawings and technical documentation
- Comparison of project specs with applicable welding codes and standards
- Selection of appropriate welding methods based on application and material
- Inspection and approval of base materials and consumables
- Verification of cutting, welding, and heat treatment equipment
- Evaluation of welders and operators, including certification checks
- Assessment of inspection facilities and testing readiness
This stage lays the foundation for successful welding by eliminatinguncertainties and aligning execution with regulatory and project-specificrequirements.
2. In-Process (During Welding)Inspection
Once welding begins, continuous monitoring is essential to detect processdeviations and maintain quality control in real time.
Key Steps in In-ProcessWelding Inspection
- Visual inspection of prepared weld joints and nearby surfaces for cleanliness and defect prevention
- Monitoring for common weld issues such as cracks, porosity, or shell imperfections
- Ensuring proper use of welding jigs, clamps, and fixtures for alignment and distortion control
- Verification of electrode storage and handling conditions, especially for low-hydrogen electrodes
- Supervision of qualified welders and assessment of their in-process performance
- Control of interpass cleaning (slag removal) and joint preparation between passes
- Monitoring of preheat conditions and maintenance of specified interpass temperatures
This stage ensures immediate quality feedback and enables correctionsbefore defects become embedded or hidden.
3. Post-Welding Inspection
After welding is complete, final inspection confirms the mechanical and structuralintegrity of the welded joints. It also verifies that the work meets allquality criteria and is fit for its intended use.
Goals of Post-WeldingInspection
- Evaluate the mechanical properties and durability of the welded joint
- Ensure structural conformity with technical specifications and end-use requirements
Post-weld tests fall into two categories:
A. Destructive Testing (DT)
Destructive Testing involves physically altering or breaking test samplesto assess material strength and behavior. These tests are often performed onsample coupons rather than the final structure.
Common DTMethods Include:
- Tensile Test – Measures the material’s strength under pulling force
- Bend Test – Assesses ductility and soundness
- Impact Test – Determines resistance to sudden force (e.g., Charpy test)
- Hardness Test – Measures surface hardness and resistance to deformation
- Corrosion Test – Evaluates performance under corrosive environments
- Etch Test – Reveals weld structure through chemical etching
B. Non-Destructive Testing(NDT)
Non-Destructive Testing allows for quality assessment without damaging thewelded component. NDT techniques are widely used to detect surface and internaldiscontinuities while preserving the integrity of the part.
Common NDTMethods Include:
- Visual & Optical Testing (VT) – First-level surface inspection using magnifiers and weld gauges
- Radiographic Testing (RT) – X-ray imaging to detect internal flaws
- Ultrasonic Testing (UT) – High-frequency sound waves identify subsurface defects
- Magnetic Particle Testing (MT) – Locates surface and near-surface cracks in ferromagnetic materials
- Dye Penetrant Testing (PT) – Highlights surface-breaking defects with visible or fluorescent dyes
- Leak Testing – Assesses the sealing capability of welds, especially in pressurized systems
Conclusion
Welding inspection is a multi-step, technically rigorous process thatprotects structural integrity and operational safety. By carefully inspectingwelded joints before, during, and after the process, InsperiaSolvex helps clients minimize risk, meet international quality standards,and extend the service life of their welded components.
Contact Insperia Solvex today to learn more about our certified weldinginspection services and how we can support your next project with unmatchedprecision and professionalism.